Entire production activity is a series of processes. Starting from raw material to the production of finished product, there is a large number of intermediate processes which take place in a production facility. Each such intermediary process leading to finished product must be predefined. All these processes must be standardized to ensure reliability, predictability and measurability of the production activity. So, each process must be designed carefully. The organized compilation of all the processes within a company forms the Operations Manual of the company. Following are some guidelines about how we can prepare Operations Manual for our company:
• Make a list of all the processes which are carried out in the company in various departments from time to time.
• Break up each process into sub-processes, if any.
• Prepared a Standard Operating Process (SOP) document for each process (or sub-process).
• In the SOP, note down all the steps for each such process, the position (designation) and the department responsible for carrying out each step.
• Recheck and confirm the sequence and appropriateness of each step.
• Audit the actual operations against the SOP, to confirm the correctness of the SOP.
• We must regularly recheck process specifications and modify them if required, in order to improve the process. Make changes in the SOP, if any step in the process changes. Keep the Operations Manual up-to-date by regularly updating it.
• Train the workers to work as per the Operations Manual.
(Expert advice to GROW your business wherever you are, whenever you want.
SMEBusinessGuide.com… https://goo.gl/E3pfoQ)
WHAT YOU CAN READ NEXT
NEXT POST:
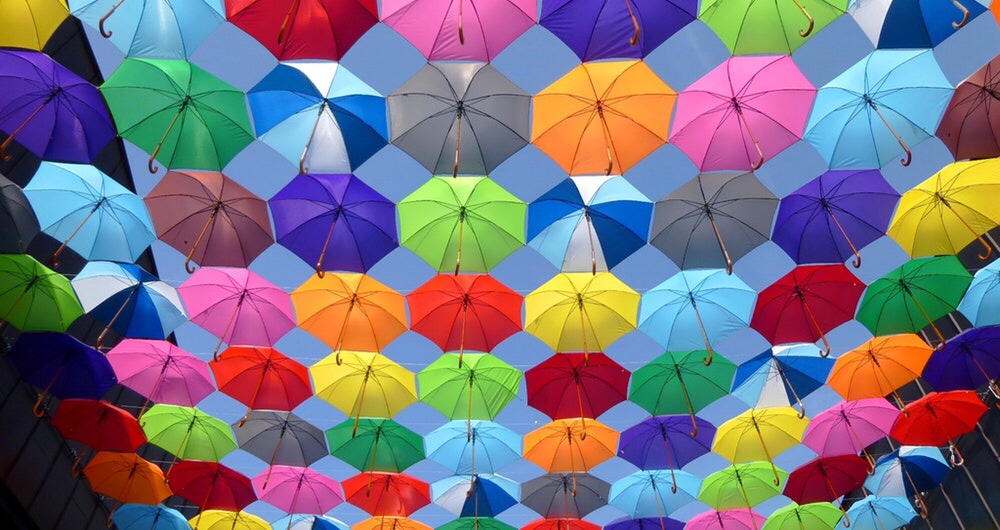
Production Planning – Standards Design
PREVIOUS POST:
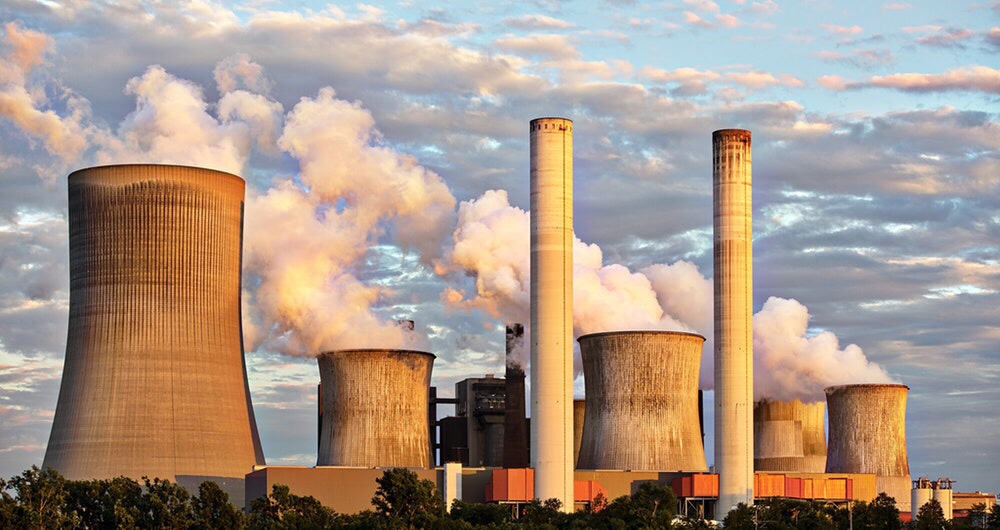
Production Planning – Production Facility Design